全自動ICP刻蝕系統以其高效、精確、自動化的特點,在半導體、光電子、MEMS等領域得到廣泛應用。隨著技術的不斷進步,其在精度、效率和智能化方面將進一步提升,推動更多高精密制造領域的技術發展。
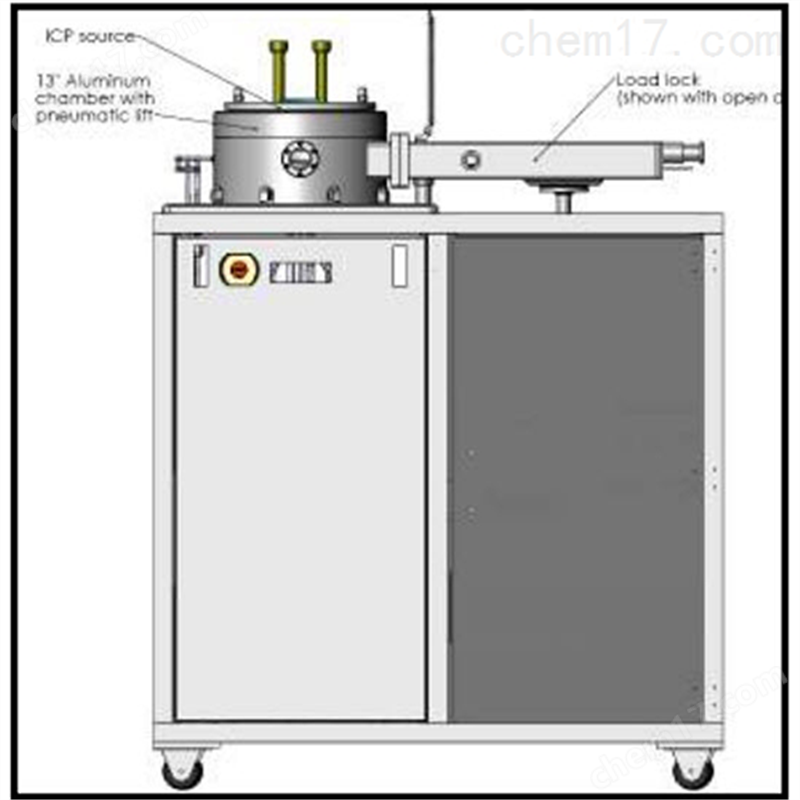
1.預處理與參數設定
操作人員通過觸摸屏或計算機界面輸入刻蝕工藝所需的參數,如氣體流量、壓力、功率、刻蝕時間等。這些參數會直接影響到等離子體的產生與穩定性,從而影響刻蝕效果。
2.氣體流量與等離子體的調控
系統會根據設定的參數自動調節氣體流量與壓力,確保等離子體源穩定產生。能夠通過傳感器實時監控等離子體的狀態,自動調整工藝參數,以維持最佳的刻蝕條件。
3.刻蝕過程的實時監控與反饋
系統配備多種傳感器,如氣體流量傳感器、壓力傳感器、溫度傳感器等,可以實時監控刻蝕過程中的各項數據。若發現任何異常,系統會自動調整或者發出報警信號,確保刻蝕過程的安全與精確。
4.自動化操作與維護
在全自動化模式下,操作人員只需進行初步的設定,系統便能夠全程自動化執行刻蝕任務。系統還配備了自我清潔和維護功能,能夠定期檢查和清理關鍵部件,減少人為操作失誤,提高生產效率。
全自動ICP刻蝕系統的關鍵技術:
1.高密度等離子體源技術
高密度等離子體源是核心技術之一。通過高頻電源激發,ICP系統能夠產生密度高達10¹?–10¹²顆/cm³的等離子體。這種高密度的等離子體能夠在較短的時間內高效去除材料表面的多余部分,保證刻蝕的高精度。
2.精確氣體流量控制技術
精確的氣體流量控制是實現高選擇性刻蝕的關鍵。配備了高精度的氣體流量控制器,能夠精確調節不同氣體的比例,以適應不同刻蝕需求。通過調節不同氣體的流量,系統可以實現對不同材料的選擇性刻蝕。
3.實時反饋控制系統
實時反饋控制系統能夠根據刻蝕過程中的各種變化,及時調整工藝參數。例如,當發現等離子體的密度下降或氣體流量不穩定時,系統會自動調整功率或氣體配比,確保刻蝕過程始終在最佳條件下進行。
4.高精度監控與診斷系統
通常配備先進的監控與診斷系統,能夠實時檢測刻蝕過程中的各項數據,包括溫度、壓力、氣體流量等,確保工藝的穩定性。該系統還能夠自動診斷設備故障,提前預警,避免設備停機或損壞。